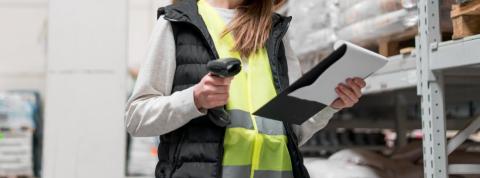
Logistics: definition and differences with supply chain management
Logistics is a cornerstone of business operations, ensuring that resources, goods, and services are effectively managed and delivered. While the term is often confused with supply chain management, it has distinct characteristics and roles within an organization.
This article explores the definition of logistics, its types, and its purposes while clarifying the primary differences with supply chain management. For professionals aiming to enhance their expertise in this critical area, advanced programs like the Master in Supply Chain Management and Logistics are invaluable.
What are the logistics of a company?
Logistics refers to the planning, implementation, and control of the efficient movement and storage of goods, services, and information from their point of origin to their final destination. It is a vital component of any business, impacting customer satisfaction, operational efficiency, and overall profitability.
Efficient organization ensure that businesses can meet market demands while maintaining quality and timeliness. This aspect of operations management focuses on delivering the right products to the right place at the right time, a goal that underpins successful supply chains.
What are the main purposes and features of logistics?
The logistics department in a company is responsible for ensuring the smooth flow of operations by coordinating resources, optimizing transportation, and managing inventory. Below are the main purposes:
- Efficient Resource Management: Logistics ensures the right resources are available at the right time and place. By streamlining supply and distribution processes, companies can meet their production and sales goals efficiently.
- Cost Optimization: By employing strategies such as route planning, bulk shipping, and technology integration, organization helps reduce operational costs. For instance, automating inventory management minimizes human error and prevents overstocking or understocking issues.
- Enhanced Customer Satisfaction: Logistics ensures that customers receive their orders on time and in good condition. This not only builds trust but also encourages repeat business.
Key features of logistics include:
- Real-time Tracking and Visibility: Modern employs technologies like GPS and RFID to provide real-time updates, ensuring transparency and accountability.
- Flexibility and Scalability: Logistics systems are designed to adapt to fluctuating market demands, enabling businesses to scale operations effectively.
- Integration with business processes: Logistics works closely with other departments such as production, marketing, and finance, ensuring seamless operations across the organization.
In summary, logistics serves as the backbone of any business by aligning resources, managing costs, and ensuring a positive customer experience. Companies with well-optimized systems are better equipped to respond to challenges and seize opportunities in their industries.
What are the different types of logistics?
Logistics encompasses a variety of specialized areas, each playing a crucial role in business operations. Below are the main types of logistics and their unique functions:
Business
This type focuses on the internal management of resources within a company. It ensures that all departments, from procurement to production, work seamlessly to achieve the organization’s objectives. Effective business logistics is critical for aligning operations with strategic goals.
Strategic
Strategic logistics involves long-term planning to enhance the efficiency and effectiveness of supply chains. This type focuses on infrastructure development, technology adoption, and collaboration with key stakeholders to maintain a competitive edge.
Distribution
Distribution logistics deals with the movement of finished goods from production facilities to end consumers. It involves transportation management, order fulfillment, and last-mile delivery, all of which are critical for ensuring customer satisfaction.
Storage
Also known as warehouse logistics, this type involves the storage, handling, and management of goods. Efficient storage ensures that inventory is easily accessible, reducing delays and maintaining product quality.
Supply
Supply logistics focuses on acquiring the raw materials and components necessary for production. It ensures that resources are procured efficiently, minimizing costs and delays. This type plays a key role in supporting production schedules and maintaining supply chain continuity.
What are the main differences between logistics and supply chain management?
While logistics and supply chain management are closely related, they differ significantly in their scope, focus, and objectives. Understanding these differences is essential for professionals aiming to optimize operations and ensure seamless business performance.
- Scope of Operations
Logistics primarily deals with the efficient movement, storage, and distribution of goods within a company or between businesses and customers. Its focus is on specific processes such as transportation, warehousing, and inventory management.
In contrast, supply chain management encompasses a broader scope, involving the coordination of multiple activities across the entire supply chain. This includes sourcing raw materials, manufacturing, distribution, and customer service. Supply chain management ensures that all parts of the supply chain work together cohesively to meet market demands. - Strategic vs. Tactical Focus
Logistics tends to have a more tactical focus, concentrating on day-to-day operations and short-term goals. For instance, managers are responsible for ensuring on-time deliveries, managing inventory levels, and optimizing transportation routes.
Supply chain management, however, has a strategic focus. It involves long-term planning to align supply chain activities with the company’s overarching business goals. This includes forming partnerships, implementing sustainability practices, and adopting innovative technologies to improve efficiency. - Key Objectives
The primary objective of logistics is to deliver goods and services to customers efficiently, cost-effectively, and on time. It focuses on optimizing internal processes to enhance customer satisfaction and reduce costs.
Supply chain management’s objectives are broader, aiming to create value across the entire supply chain. It seeks to build strong relationships with suppliers, improve overall supply chain resilience, and ensure that all stakeholders collaborate effectively. - Technology and Integration
Logistics relies heavily on technologies like GPS tracking, warehouse management systems (WMS), and transportation management systems (TMS). These tools are designed to streamline operations and provide real-time visibility into logistics processes.
Supply chain management integrates these technologies with additional tools such as enterprise resource planning (ERP) systems and advanced analytics. This integration ensures end-to-end visibility, enabling better decision-making and coordination across the supply chain. - Examples in Practice
- Logistics: A team focuses on planning the best transportation routes to deliver products to customers in the shortest possible time.
- Supply Chain: A supply chain management team collaborates with suppliers, manufacturers, and distributors to ensure raw materials are procured on time, production schedules are met, and goods are delivered to markets efficiently.
By understanding these differences, businesses can ensure that both logistics and supply chain management are effectively aligned to achieve operational excellence.
Conclusion
Logistics and supply chain management are vital components of any successful business, but they serve different purposes. Logistics focuses on the tactical aspects of managing goods and resources, while supply chain management oversees the strategic integration of all supply chain activities. Together, they form the backbone of efficient and competitive operations.
For professionals looking to deepen their knowledge and skills in these areas, pursuing specialized training like the Master in Supply Chain Management and Logistics is a step toward becoming an industry leader. Understanding the nuances of logistics and supply chain management will empower you to optimize operations, drive innovation, and achieve long-term business success.